

The participants learn how to improve the collaboration of casting designers with the downstream production chain. This training enhances the proficiency of the casting designers to come up conceptual and technical solutions. This also allows a direct comparison with CT measurements. Magma training imparts casting process simulation skills. Thus, for the first time, all potential defects in the casting (Caused by both air entrapment and shrinkage porosity) can be evaluated using a single result. MAGMAproject is the metal casting simulation project engineering service that we provide to our existing & non-existing clients who are seeking for a comprehensive solution on process optimization using our well proven MAGMA APPROACH methodology together with our experts who are experienced foundry engineers, metallurgical specialists and mechanical engineers. In addition the prediction of feeding during the intensification phase has been improved. The corresponding masses of air and well as the effectiveness of the venting conditions can be quantitatively tracked over time using calculated curves. It is possible to consistently evaluate the quality of the tooling design and the process conditions over the course of a project, even under changing situations. In the new “Air” result, the amount of air in the cavity and in the melt is visualized quantitatively and allows complete assessment over the entire filling process.

The mass balance of air in the cavity and the transport of entrapped air can reliably predicted using MAGMASOFT® 5.5.
#MAGMASOFT SIMULATION SOFTWARE#
Tooling and process design therefore focus very strongly on reducing porosity due to entrapped gases and shrinkage. MAGMA is a worldwide leader in developing and providing software for casting process simulation and virtual optimization. In high pressure die casting, casting defects due to entrapped air combined with shrinkage porosities are major causes for scrap. The new feeding model is available for all types of cast iron: Grey, ductile and compacted graphite iron. Thus, both metal quality and inoculation state influence feeding and shrinkage formation in the casting. The software calculates local metal transport in partially solidified regions of the casting and the resulting ability to feed the solidifying iron. Pressure differences in the metal are created through the combination of metallostatic pressure, local austenite shrinkage and graphite precipitation and the rigidity of the mold. The “heart” of the optimized MAGMAIron module is the SMAFEE feeding algorithm. With this digital rendering, the manufacturer will be able to optimize and evaluate. In fact, before the process even begins, MAGMAsoft displays realistic, predictive, and analytical 3D simulation of your product.
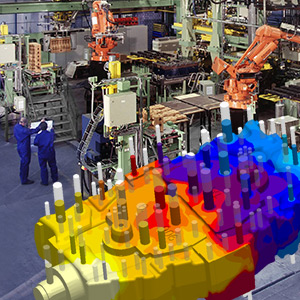
Consequently utilizing the methodology of virtual Design of Experiments and Autonomous Optimization, robust process. MAGMAsoft Die Cast Process Simulation software boasts realistic mapping of the entire process, from the first step to the last. MAGMASOFT ® is the comprehensive and effective optimization tool for improving metalcasting quality, optimizing process conditions and reducing production costs.
#MAGMASOFT SIMULATION SERIES#
The impact of the flow on the resulting temperature profile influences the feeding behavior both, large castings and in series production. Simulation and virtual optimization of casting processes. In addition, thermal convection during solidification is now calculated as a standard for iron castings. With the innovative SMAFEE feeding algorithm, the influence of melt quality, inoculation practice and local pressure distributions on porosity development is even better taken into account. Completely new capabilities are available to iron foundrymen to consider the effects of metallurgy and metal treatment on solidification and feeding behavior.
